Metallurgical Microscope
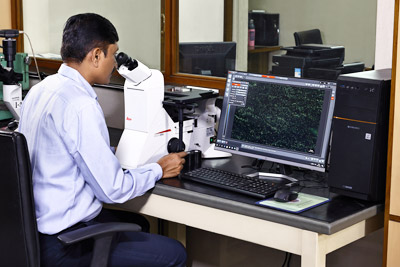
Turbo uses high quality bearing steel SAE 52100 or 100 Cr6 of internationally acceptable grade to make the bearing components. All components are inspected by German Make Leica metallurgical microscope to ensure macro and micro structure of all the bearing components as per SEP 1520 German specification chart. High resolution HD camera-FLEXACAM C3, is connected to microscope to interface it with image analyzing software to catch, analyze and share high quality digital images. Microstructure checking to maintain consistent quality as per standard norms considering the following:
- Spheroidized structure.
- Amount of perlite.
- Inclusion rating.
- Carbide network.
- Carbide streaks (bandings).
Micro Structure
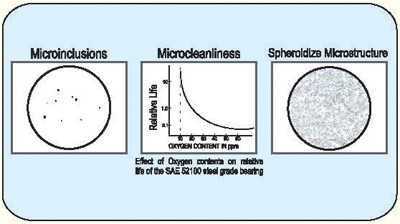
The grade of steel used is SAE-52100 / 100 Cr 6 (modified) bearing steel of international acceptability.
Bearing steel is used only after ensuring macro (for non metalic inclusion rating/cleanliness) and microstructure, as per standard specifications to ensure the long life of bearings.
Profile Projector
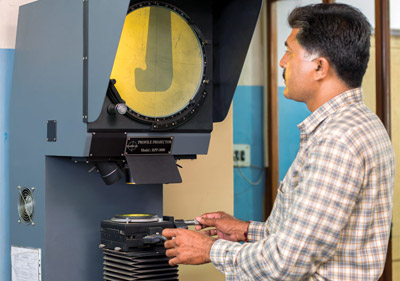
We have profile projector, which is used for checking/controlling the profiles of grooves, butting radius, etc., at turning stage.
Standards Room
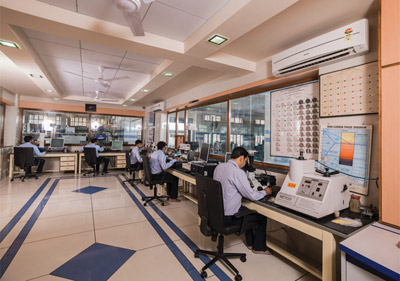
Our Standards Room has all the facilities of quality appraisal equipment, such as TALYROND - Roundness Testing machine, FORM TALYSURF - profile and surface finish testing machine etc. imported from world renowned make - Taylor Hobson, U.K.
We also have other inspection facilities, such as Bearing Eccentricity tester, Dial Calibration Instrument and Residual Magnetism Tester etc.
Metrology Lab - Universal Measuring Machine
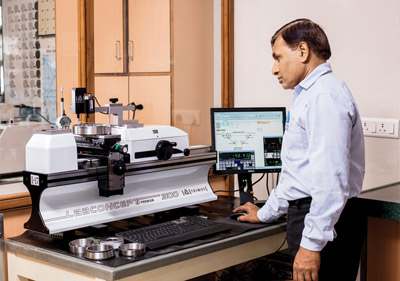
TURBO has installed a Universal measuring machine from TRIMOS - Switzerland. This machine gives absolute value of internal dimensions, external dimensions and angles of rings and rollers, measured as per international standards. This machine is used to calibrate the bearing components as per designed dimensions.
Talyrond
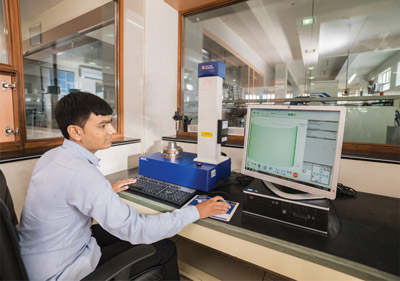
Talyrond - Taylor Hobson Ltd. (U.K.) make: This world renowned quality appraisal equipment is used for checking the roundness, squareness, concentricity, cylindricity, flatness and coaxiality of bearing components, which ensures running accuracy for longevity life of TURBO bearings.
Form Talysurf
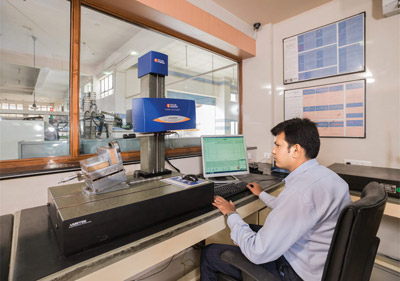
We have latest version of Form Talysurf (Form and Surface Finish Measuring machine) from world famous Taylor Hobson Ltd. (U.K.). This machine is used for checking Micro geometry. It evaluates parameters like Form geometry and surface finish of components. This control helps for improving the quality and product performance in the field. Our R& D continuously makes improvements in these accuracy parameters of races & rollers, to enhance field performance of TURBO bearings.
Roller Grouping Machine
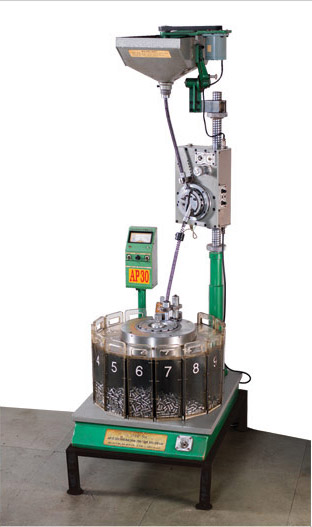
We have imported automatic roller grouping machines for Tapered rollers. These machines have facility to group the rollers within 1 micron grading. The close grading gives uniform load distribution in the bearings for longer life.
Bearing Noise Level & Vibration Tester
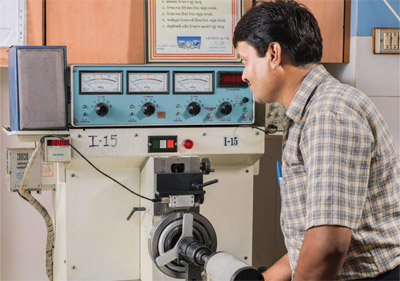
We have imported noise level testing machines, which are used for checking the noise & vibration of ball and roller bearings. These equipments have low band, medium band and high band vibration measuring facility, which enables to identify the control of quality parameters of various bearing components. They help in upgrading the bearing performance.
Magnetic Crack Detection
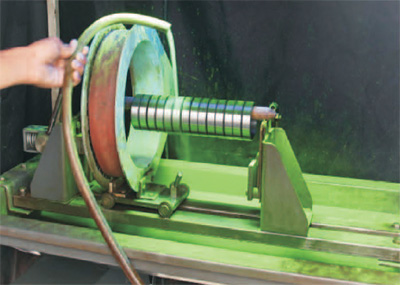
We have Magnetic Particle Inspection (MPI Testing) Machine, which is widely used for non-destructive testing of the bearing components, to identify the surface cracks. The test is performed by spreading fine Ferrous-oxide particles with high magnetic permeability (mixed with a liquid media), over the surface of the test part & simultaneously magnetising the component with a strong magnetic field, created by passing an electric current through a coil. The Ferrous oxide particles are attracted to the leakage field (crack), which can be visually detected under the Ultra Violet lighting. This test is fast and reliable process, where indication of surface defects is visible directly on the test piece surface.